
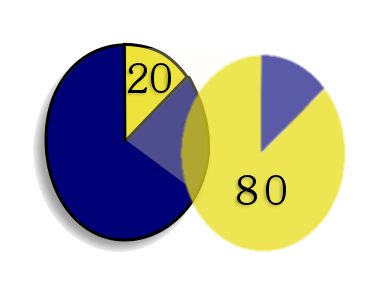
Quickly helps identify troubleshooting areas for change management Background and Methodology of Pareto Analysis Improves efficiency, quality of work, and decision making Helps organize pre-existing data to make it more meaningful () (does not apply to future scenarios)Īllows you to address major issues before they can grow in proportion (relatively compares data values) It helps prioritize problem-solving for root causes by process of elimination in descending order of impact (cannot be used to determine root cause)
#80 20 principle lean drivers
If you see a flat curve ( ) or no main 2 or three drivers to work on, then either data is lacking, requires re-categorization, or is not showing the right driver first. The 80/20 principle is not fixed, rather is a generic number to determine the few most impactful driving factors for Root Cause Analysis, allowing you to prioritize problem-solving. For example:Ģ0% of your products/services generate 80% of your profitsĨ0% of Customer complaints come from 20% of service issuesĢ0% of viruses cause 80% of system crashes/errorsĨ0% of a company’s revenue comes from 20% of its clients. This principle can be applied across multiple circumstances as a decision-making tool, provided significant data is available to evaluate in a given time frame. Utilized for many business applications, especially Quality Assurance metrics, it allows to constantly identify the highest problem driver, and address them in a focused manner to improve the overall procedure. One of the Lean Six Sigma methodologies for Process Improvement Pareto defines that 80% of problems in any process can be effectively managed by addressing 20% of the factors causing it. Known by multiple names such as the Pareto Principle, the 80/20 rule, and the law of the vital few and trivial many Pareto Analysis is a strategic technique applied to logically identify the cumulative impact of a problem stemming from its frequency and multiple causes.
